Kokereitechnik - Ein kleiner Einblick
Die schwarze Seite
Zum Inhalt:
Der Koksofen
Das Heizgas
Der Ofenbetrieb
Der Verkokungsprozeß
Drücken und Löschen des Kokses
Der Umweltschutz
Rückblick - Die Entwicklung der Koksindustrie.
Man kann wohl ohne weiteres sagen, daß es ohne Koks niemals zu dem Eisen- und Stahlboom gekommen wäre, der dem Ruhrrevier ab Mitte des 19. Jahrhunderts den Aufstieg zum Großindustriegebiet sicherte. Das Kokereiwesen spielte eine bedeutende, aber meist zu wenig geachtete Rolle bei der stürmischen Entwicklung. Denn die Steinkohle ist zur Verhüttung von Eisenerz in unveredelter Form ungeeignet, d. h.:Ohne Koks geht es nicht!
Steinkohle backt im Hochofen zusammen und verhindert einen guten Ofengang. Der Koks erfüllt demnach im Hochofen mehrere Aufgaben: er liefert den Heizkohlenstoff für die Erzeugung der Schmelz- und Reduktionswärme, den Kohlenstoff für die Reduktion der eingesetzten Eisenerze und den Kohlungskohlenstoff für die Aufkohlung des Eisens (Eisenkarbidbildung Fe3C), die eine Schmelzpunktabsenkung bewirkt. Ebenso muß der Koks widerstandsfähig gegen Druck sein, da er die Möllersäule trägt (Möller = die eingesetzten Stoffe im Hochofen), sowie schwefel- und aschearm, sonst erhält man ein Roheisen minderer Qualität.
Der Koks wurde für die Hochofentechnik von Eisenhüttenmännern erfunden, angespornt durch den Umstand, daß, durch den riesigen Bedarf bedingt, Holzkohle immer teurer wurde und Bäume immer rarer. Für die Erzeugung von 1 Tonne Roheisen benötigte man seinerzeit ca. 30 Tonnen Holz!
Etwa im Jahre 1630 gelang es Dud Dudley auf den Eisenwerken seines Vaters Lord Edward in Worcestershire Steinkohlenkoks herzustellen. Er kam auf die Idee die Steinkohle genau wie das Holz zunächst einer Vorbehandlung zu unterziehen um den richtigen Brennstoff für den Hochofen zu gewinnen. Soweit bekannt ist, gelang es ihm auch aber der Erfolg und die Anerkennung blieben aus - er war seiner Zeit zu weit voraus.
Etwa hundert Jahre später, im Jahre 1709, erblies Abraham Darby (I) Steinkohlenroheisen auf seiner Hütte zu Coalbrookdale (Shropshire).
Aber er nutze und vervollkommnete die Erfindung nicht und gab auch sein Wissen nicht weiter. Als sein Vater 1717 verstarb übernahm sein Sohn Abraham Darby (II) neunzehnjährig den väterlichen Betrieb. Er experimentierte mit der Meilerverkokung der Steinkohle so lange, bis es ihm gelang einen ordentlichen stückigen, schwefelarmen Koks zu erzeugen. Ebenso unermüdlich arbeitete er an seinen Experimenten brauchbares Roheisen zu erschmelzen. Und - die Mühe lohnte sich. Unter seiner Führung stieg Coalbrookdale zum führenden Hochofenwerk Englands auf.
So wie auf vielen anderen Gebieten auch, im Maschinenbau, in der Entwicklung der Textilverarbeitung, überhaupt in der Überführung manueller Tätigkeiten in industrielle Größenordnungen blieb es also den Engländern vorbehalten, das Problem der Steinkohlenverkokung und das Verhütten der Eisenerze mit Koks zur Zufriedenheit zu lösen.
Erfolgte also zunächst die Erzeugung der Kohle wie die des Holzes in offenen Meilern ging man sehr bald zu geschlossenen Retorten über. Die ersten geschlossen Koksöfen wurden 1856 in Frankreich von Knab errichtet, jedoch befanden sich die Flammzüge bei diesem Ofentyp nur unterhalb der Öfen. Erst Carvès führte die Seitenkanäle ein. Neben diesem frühen Ofentyp von Knab-Carvès kamen weitere erfolgreiche betriebene Ofentypen von Bauer, Collin, Coppée, Semet-Solvay und Appolt hinzu. Es gab Ofentypen wie die Flammöfen (ohne Nutzung des Destillationsgases), später die Abhitzeöfen mit Nutzung der Destillationsgase. Wobei gesagt werden muß, daß schon bei den alten Bienenkorböfen versucht wurde, die Destillationsgase zu nutzen. Der verbreiteste Ofentyp war damals der Otto-Hoffmann-Ofen. In dieser Zeit kamen auch die ersten Rekuperativöfen auf: der Vorläufer des Regenerativofens. Mit diesem Ofentyp versuchte man erstmals die Abwärme der Verbrennungsgase zu nutzen. Dies gelang auch mit dem Regenerativofen.
Diese den Abhitzeöfen wärmetechnisch weit überlegen Öfen erzielten ein nicht unerheblichen Heizgasersparnis und damit eine größere Ausbeute des Koksgases. Und einen sparsamen und leistungsfähigen Ofen zu konstruieren war und ist noch heute Ziel eines jeden Ofenbauers. Im Verlaufe der Jahre haben also viele kluge Köpfe durch Verbesserungen und Neukonstruktionen die Mehrleistung der Koksöfen immer weiter gesteigert. Neben den bereits oben genannten Firmen haben noch Franz Brunck und vor allem Heinrich Koppers, Carl Still und Gebr. Hinselmann großen Anteil am Fortschritt gehabt. Heute gibt es nur noch Verbundöfen. Das sind weiterentwickelte Regenerativöfen, die wahlweise mit Stark- und Schwachgas unterfeuert werden können. Unsere heutigen Hochleistungsöfen sind daher das Produkt einer viele Jahrzehnte dauernden Entwicklungsarbeit. Das schont auch die Umwelt!
Der Koksofen.
Eine Kokerei ist nichts anderes, als eine Ansammlung von Backöfen, in denen Kohle unter Luftabschluß (!) geschmort wird. Die Seite der Kokerei, wo dies geschieht, also wo die Koksöfen stehen, nennt man "die schwarze Seite". Die Koksöfen sind meist 6 - 7 m hoch, 15 m lang und nur 0,45 m breit; etwa 35 bis 40 solcher Koksöfen werden zu einer Batterie zusammengefaßt.Der Koksofen ist in Oberofen und Unterofen unterteilt, wobei der Oberofen aus den senkrechten Heizzügen und den dazwischenliegenden Ofenkammern und der Unterofen aus den unter den Ofenkammern angeordneten Regeneratoren, Gaszuführung und Abgasableitung besteht. In den Regeneratoren wird bei Starkgasbeheizung die benötigte Verbrennungsluft durch die Abhitze vorgewärmt, bei Schwachgasbeheizung sowohl die Verbrennungsluft als auch das Schwachgas.
Eine Ofenfüllung betrug um die Jahrhundertwende etwa 6 t Kokskohle. Heute beträgt das Fassungsvermögen einer einzigen Ofenkammer der Kokerei Schwelgern fast 79 t Kokskohle! Die Kokskohle ist eine Mischung verschiedener Kohlensorten, die zusammen eine optimale Koksqualität ergeben. Die Korngröße beträgt 10 - 0 mm, der Wassergehalt etwa 10 % und der Aschegehalt 6 - 7 %.
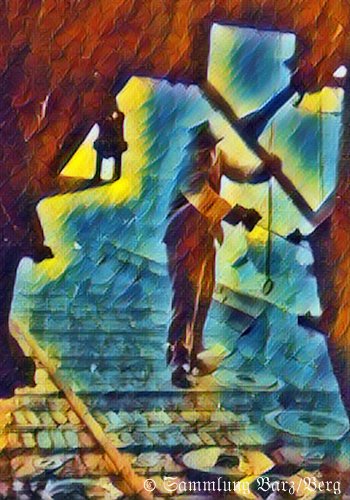
künstlerische Darstellung
(© Sammlung Barz/Berg)
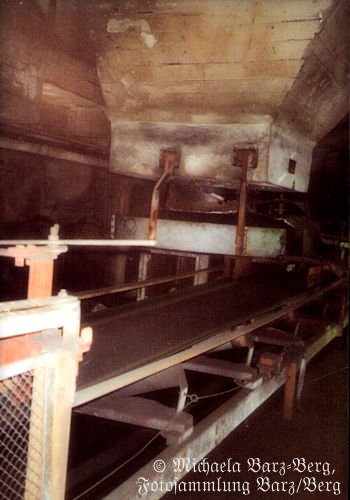
Kohlenmahl- und Mischanlage, Kokerei August Thyssen
(© Michaela Barz-Berg, Fotosammlung Barz/Berg)
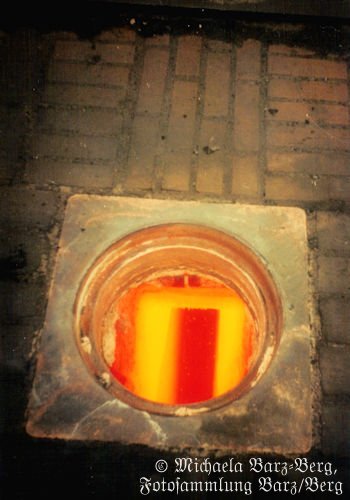
Batterie 6b, Kokerei August Thyssen, 1998
(© Michaela Barz-Berg, Fotosammlung Barz/Berg)
Heizgas.
Die Beheizung erfolgt durch Starkgas (Koksofengas) oder Schwachgas (Gichtgas bzw. Hochofengas),
das in den Heizzügen zwischen den einzelnen Ofenkammern verbrannt wird. Der Heizwert des
Gichtgases beträgt mit 1000 kcal nur etwa den vierten Teil von dem des Koksofengases.
Um einen Heizwert von 1250 kcal/m³ zu erreichen, wird dem Schwachgas noch Stahlwerkgas
und Koksofengas zugesetzt. Um diesen Heizwert konstant halten zu können wird bei Bedarf auch Erdgas
zugegeben. Auch Kohlenstaub oder Erdöl, früher zuweilen auch Teer, werden zur
Karburierung (= das Zusetzten von Stoffen um den Brennwert des Gases zu erhöhen)
des Gases verwendet.
Als Baumaterial der Öfen werden feuerfeste Steine verwendet wie Silika, Schamotte oder Silimanit.
Ofenbetrieb.
Die von den Bergwerken angelieferte Feinkohle wird in Bunker entladen und anschließend der Kohlenmischanlage zugeführt. Von hieraus gelangt die fertig gemischte Kokskohle über Förderbänder zu einem der Kokskohlentürme (KKT). Diese KKTs stehen zwischen den Batterien, so daß der auf der Ofendecke der Koksöfen fahrende Füllwagen, der jeweils eine Ofenfüllung (Charge) faßt, unter ihm leicht beschickt werden kann. In der Ofendecke sind die Füllöcher angebracht, durch die die Kohle eingeschüttet wird.Durch den Füllvorgang bilden sich Kohlen-Schüttkegel, die maschinell durch die Planierstange eingeebnet werden müssen, da sie den störungsfreien Gasabzug im Gassammelraum verhindern würden. Die Planiervorrichtung befindet sich rechts seitlich neben der Druckstange auf der Druckmaschine angeordnet.
Verkokungsprozeß.
Die Kokskohle wird nach dem Einfüllen in die von zwei Seiten beheizte Ofenkammer, deren Wände 1200° - 1350° C heiß sind, zonenweise von den Kammerwänden zur Kammermitte zu Koks umgewandelt. Dabei erweicht die Kohle ab 350° C. Zwischen 350° C und 480° C findet die Koksbildung und die Entgasung statt, ab 480° C beginnt die Wiederverfestigung und die Nachentgasung setzt ein. Der Verkokungsvorgang ist ab 900° C abgeschlossen. Eine gleichmäßige Beheizung der Heizzüge ist eine wesentliche Voraussetzung für einen gut ausgegarten Kokskuchen. Nach der Erreichung der Hälfte der Garungszeit beginnt erst in der Mittelschicht ein wesentlicher Temperaturanstieg, während sich an den Wänden bereits eine Koksschicht gebildet hat; Kohle ist ein ausgesprochen miserabler Wärmeleiter. Die beiden plastischen Zonen vereinigen sich später in der Ofenmitte und bilden die Teernaht.

Die Garungszeit beträgt, je nach Beschaffenheit der Kohle, Größe der Ofenkammer usw. etwa 20 Stunden.
Drücken und Löschen des Kokses.
Zum Ausstoßen des Kokses werden zunächst die beiden stählernen mit feuerfesten Steinen ausgemauerten Ofentüren abgehoben. Deren Gewicht beträgt ca. 5 t! Der Druckkopf der Druckmaschine durchfährt dann die Ofenkammer und drückt den Koks über den Kokskuchenführungswagen (oder eine Koksüberleitmaschine) in den bereitstehenden Löschwagen. Der glühende Koks wird sofort unter dem Löschturm gefahren. Hier wird er (ca. 21 t Koks bei 28 t Einatzkohle) mit Wasser (etwa 45 m³) abgelöscht, damit er nicht an der Luft verbrennt. Dabei verdampfen ca. 10 m³ Wasser. Dieser Vorgang verursacht die für Kokereien typischen weißen Dampfwolken, die "Löschwolken". Der geleerte Koksofen wird umgehend wieder mit neuer Kohle beschickt. Der abgelöschte Koks gleitet aus dem Löschwagen auf die Koksrampe, wo er ausdampft und dann über ein Förderband in die Kokssieberei gelangt. Hier wird er zu folgenden Sorten abgesiebt:- Großkoks über 80 mm Korngröße
- Brechkoks I 80-60 mm Korngröße
- Brechkoks II 60-40 mm Korngröße
- Brechkoks III 40-20 mm Korngröße
- Brechkoks IV 20-10 mm Korngröße
- Koksgrus 10-0 mm Korngrus
Koks ist also nichts weiteres als destillierte Kohle: ein kohlenstoffreicheres Endprodukt entsteht. Daher auch die Bezeichnug "trockene Kohlendestillation". Heute wird nur noch Hochofenkoks produziert. Gießereikoks wird heute importiert und Gaskoks, wie ihn früher zahlreiche Gaswerke hergestellt, haben gibt es gar nicht mehr. Sie sind heute Technikgeschichte. Bei diesen Betrieben, sie wurden auch häufig "Gasanstalten" genannt, war das Gas das Hauptprodukt der Erzeugung: das Stadtgas.
Der Umweltschutz.
Auch dem steigendem Umweltschutzbewußtsein wurde in den letzte Jahrzehnten mehr und mehr Rechnung getragen. Wurde früher eher aus ökonomischen Gründen darauf geachtet mit den Ressourcen hauszuhalten und z. B. Wärmerückgewinnung betrieben, wurde dies ab den 60er Jahren mehr und mehr aus Umweltschutzgründen getan. Heute sind effiziente Absauganlagen für Füllgase und Koksüberleitmaschinen mit koksseitiger Entstaubung eine Selbstverständlichkeit. Lärm- und Gewässerschutz nehmen heute hohe Stellenwerte ein, die Staubemissionen wurden auf ein Minimum reduziert, wobei die anfallenden Filterstäube und -schlämme recycelt werden.Quellennachweis:
- Dr. A. Spilker: "Kokerei und Teerprodukte der Steinkohle", Halle (Saale), 1933
- Dr. Otto Grosskinsky: "Handbuch des Kokereiwesens", Bd. I und II, Düsseldorf, 1958
- Dr. F. M. Ress: "Geschichte der Kokereitechnik", Essen, 1957
© Michaela Barz-Berg
Bild- und Textmaterial sind urheberrechtlich geschützt. Alle Rechte vorbehalten. Die Verwendung der Texte, Bilder oder Graphiken - auch auszugsweise - ohne Genehmigung des Webmasters ist strafbar.
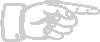