Kokerei Emil
Die Zechenkokerei Emil befand auf dem Gelände des Schachtes Emscher III des Köln-Neuessener Bergwerksvereins an der Gladbecker Straße in Höhe der gegenüberliegenden Straßeneinmündungen Teilungsweg und Johanniskirchstraße in Essen-Altenessen-Nord. Am 2. März 1903 begannen die Abteufarbeiten des Schachtes "Emil" der im Jahre 1911 zu Ehren des Generaldirektors der Gesellschaft Geh. Bergrat Emil Krabler den Namen "Schacht Emil" erhielt und fortan eine eigenständigene Schachtanlage darstellte.Um diese Zeit war auch die Errichtung einer kleinen Zentralkokerei geplant. Die Wahl des Standortes fiel auf Schacht Emil, da auf Zeche Anna nicht mehr genug Raum vorhanden war. Die Zeche Anna lag inzwischen mitten in einer Wohnsiedlung da die Bebauung mit den Jahren stark voran schritt. Auf der Kokerei Anna befanden sich zu diesem Zeitpunkt neben 60 Hüssener Abhitze-Öfen (ein von Albert Hüssener verbesserter Carvès-Koksofen) zwei Batterien Bauart Collin-Ruppert und eine Kohlenwertstoffgewinnung in Betrieb. In früheren Zeiten wurden auf Kokerei Anna Koksöfen der 1. Generation, die Schaumburger Koksöfen, betrieben.
Nach der Fertigstellung der Kokerei und der Zusammenlegung der beiden Betriebsanlagen bildeten Schacht Emil und Zeche Anna eine einheitliche Betriebsanlage. Die Kokerei nahm am 1. Oktober 1911 den Betrieb auf.
Ende des Jahres 1911 wurde daher auch die Kohlenseparation und -wäsche des Schachtes Anna stillgelegt. Schacht Anna förderte seitdem nur noch Kessel- und Deputatkohlen, die ganze übrige Förderung aus den Betrieben des Schachtes wurde mit der Grubenbahn untertage nach Schacht Emil gebracht. Mit dem Tage der Außerdienststellung des Schachtes Anna als Förderschacht stand die seit dem Jahre 1873 betriebene Kokerei ohne Kohlen, daher erfolgte die Stillegung und 1912 der Abbruch.
Am 22. Dezember 1930 fand die Fusion des Köln-Neuessener-Bergwerksverein mit der "Eisen und Stahlwerk HOESCH AG", mit welcher seit 1. Juli 1920 eine Interessengemeinschaft bestand, zu HOESCH-Köln Neuessen AG für Bergbau und Hüttenbetrieb" statt. Am 1. Juli 1935 wurden die Betriebsanlagen Anna, Emil, Carl und Emscher zu der Förderanlage "Emil-Emscher" zusammengefaßt.
Die beiden Batterien aus dem Jahre 1911 bestanden aus 28 Koppers Abhitze-Koksöfen und 28 Koppers-Regenerativ-Koksöfen. An Nebenprodukten wurden Teer, schwefelsaures Ammoniak und Rohbenzol gewonnen. Im Jahre 1927 wurde diese kleine Kokerei abgebrochen.
Dreizehn Jahre später wurde der Entschluß gefaßt, im Anschluß an die bestehende Ofenanlage Batterien I - IV, den Bau von neuzeitlichen 90 Unterbrenner-Verbund-Koksöfen System Didier-Kogag-Hinselmann zu errichten.
Der Bau der drei neuen Batterien mit 3 dazugehörigen Schornsteinen erfolgte im Anschluß an den neu errichteten Kohlenturm für 3000 t Nutzinhalt nördlich der noch betriebenen Batterie I. Am Kohlenturm wurde östlich ein neuer Löschturm angeordnet.
Die Didier-Kogag-Hinselmann-Verbundöfen hatten folgende Abmessungen:
Ofenhöhe bis zum Scheitel Mittlere Ofenbreite Konizität Länge zwischen den Türen Länge zwischen den Ankerständern Ofenmittenabstand Stärke der Batteriedecke |
4150 mm 450 mm 60 mm 11950 mm 12700 mm 1150 mm 1000 mm |
Folgende Beschreibung zum Betrieb der Öfen kann dem Bauantrag entnommen werden:
"Das Heizgas tritt durch die Düsenleitung (a) und weiter durch die Düsen in die Brenner ein. Die Verbrennungsluft tritt durch die Öffnung 1 in die Wärmespeicher und wird hier vorgewärmt. Und gelangt durch den Luftverteilungskanal in die Durchtritte zu den einzelnen Brennerstellen der Heizzüge.
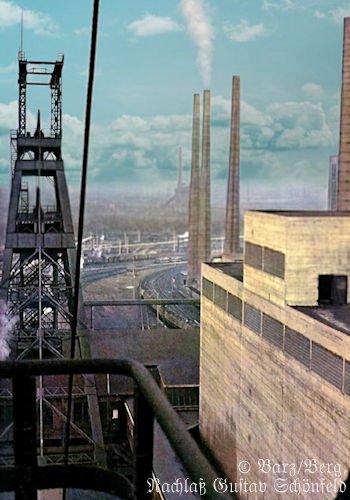
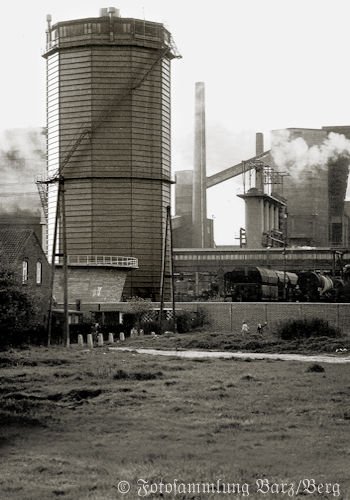
(© Fotosammlung Barz/Berg)
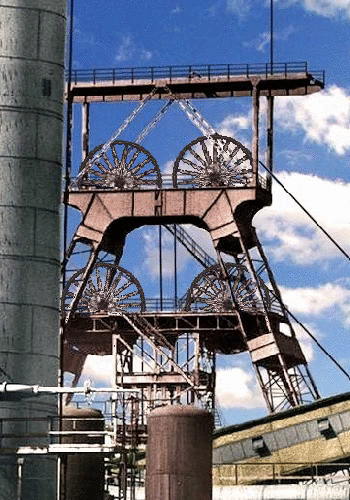
Colorierte Animation, etwa 1969
(© Fotosammlung Barz/Berg)
Die Verbrennungsgase durchstreichen den oberen Horizontalkanal, gehen durch die Heizzüge der anderen Ofenhälfte zu den Wärmespeichern, an die sie ihre Wärme bis auf die für den Kaminzug erforderliche Temperatur abgeben und gelangen von dort durch die Abhitzekrümmer und den Abhitzekanal zum Kamin.
Die Regelung der Verbrennungsluft für die einzelnen Heizwände geschieht an der Durchtrittsstelle vom Wärmespeicher in den Sohlkanal durch die hier angeordneten Schieberchen, die von den Ofenköpfen aus leicht zu erreichen sind. Die Beaufschlagung der einzelnen Heizzüge wird durch die Schieberchen an der Durchtrittsstelle von den Heizzügen zum Horizontalkanal geregelt. Diese Schieberchen sind durch die Durchbrechungen in der Ofendecke leicht einstellbar und zu überwachen.
Die Gaszufuhr für jeden einzelnen Ofen bzw. für die mittleren Heizzüge wird durch besondere Regelhähne in den Gaszuführungsleitungen geregelt."
Nach Inbetriebnahme der Batterien A,B und C und wurden die zunächst die alten Batterien I und II stillgelegt und abgebrochen und die Batterien D und E errichtet. Die zuletzt errichtete Batterie F verfügte nur über 28 Koksöfen. Durch die Kriegswirren bedingt verzögerte sich die Neuerungsmaßnahmen erheblich, viele Umbaumaßnahmen wurden daher auch erst nach Kriegsende durchgeführt. Im März 1945 mußte gar aufgrund schwerer Schäden die komplette Kokerei stillgelegt werden. Nach notdürftigen Reparaturen wurde sie aber noch im selben Jahr wieder in Betrieb genommen.
Das produzierte, gereinigte Gas, seinerzeit "Stadtgas" genannt wurde an das Ruhrgasnetz abgegeben, des weiteren vielen als Kohlenwertstoffe Teer, Rohbenzol, Schwefelsäure, Ammoniumsulfat sowie verdichtetes Ammoniakwasser an.
Im Rahmen der Konzernentflechtung nach dem Zweiten Weltkrieg wurden die Hoesch-Zechen aus der Verwaltung der HOESCH AG herausgelöst und die Kokerei Emil der Altenessener Bergwerks-AG unterstellt.
Die Versuchkokerei.
Im März 1957 stimmte der Vorstand des Steinkohlenbergbauvereins in einer Sitzung dem Vorhaben eine Versuchsanlage beim Steinkohlenbergbauverein zu errichten zu.Die Anlage bestehend aus fünf technischen Versuchsöfen wurde im folgenden Herbst und Winter errichtet und ermöglichte wärmetechnische Untersuchungen an modernen Hochleistungsöfen. Es sollten zum Beispiel die Auswirkungen bei Änderung der Heizzugtemperatur oder der Einfluß des Wassergehaltes der Kokskohle untersucht werden um so bessere Voraussetzungen für eine betriebswirtschaftliche optimale Gestaltung eines Kokereibetriebes zu schaffen.
Vervollständigt wurde die Versuchanlage durch eine Rohgaskondensation und den Zubau einer Kokssieb- und verladeanlage.


Das Konzessionsgesuch zur Errichtung der Kokssieb- und verladeanlage reichte die Heinrich Koppers GmbH, Essen, im Mai 1959 ein. Der Zubau wurde aus Mitteln des Landes Nordrhein-Westfalen errichtet. So konnten auch Untersuchungen zur Qualität des Kokses und der Kohlenwertstoffe und die Abhängigkeiten untereinander erfolgen wie zum Beispiel sich die Höhe des Wassergehaltes in den Kokskohlen auf die Beschaffenheit des Kokses auswirkt.
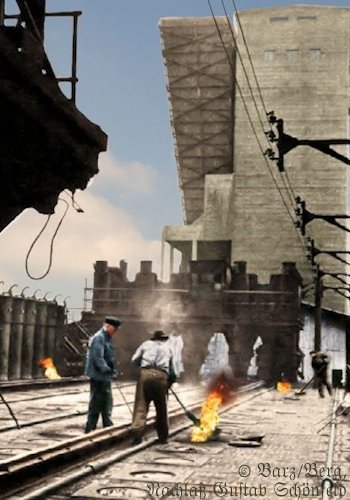
colorierte Darstellung.
(© aus dem Nachlaß Gustav Schönfeld)
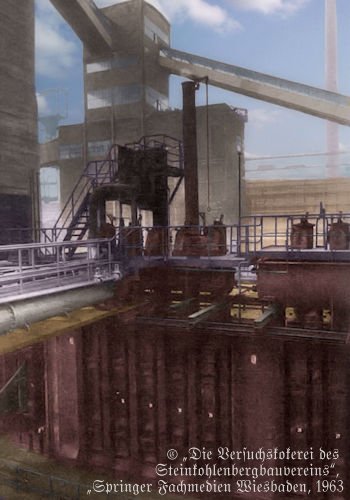
(© Die Versuchskokerei des Steinkohlenbergbauvereins,
Springer Fachmedien Wiesbaden, 1963)
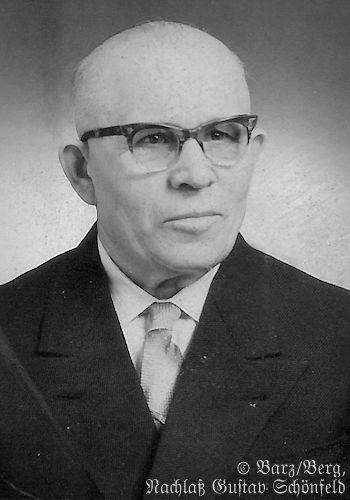
Die aus fünf Öfen bestehende Ofengruppe bestand aus halbgeteilte Regelstrom-Unterbrenneröfen. Ein 1,5 m breiter gemauerter Zwischenkopf Verband die Öfen mit der benachbarten Ofengruppe, die aus 28 kopfbeheizten Regelstromöfen bestand, der Batterie "F". Beide Ofengruppen hatten einen gemeinsamen Abgaskanal.
Maße der Versuchsöfen
Länge zwischen den Ankerständern Länge zwischen den Türstopfen Scheitelhöhe der Kammer Füllhöhe Kammerbreite Maschinenseite Kammerbreite Koksseite Mittlere Kammerbreite Stärke der Ofendecke Ofenteilung Ofeninhalt |
12700 mm 11880 mm 4150 mm 3850 mm 420 mm 480 mm 450 mm 1000 mm 1150 mm 20,65 cbm |
Die Heizwände waren mit 30 Heizzüge unterteilt wobei 16 Heizzüge abwechselnd auf der Maschinenseite und 14 auf der Koksseite beflammt wurden, wobei jeder Heizzug zwei Gaszuführungen hatte die gleichzeitig oder einzeln mit Heizgas beaufschlagt werden konnten. Um den Verkokungsfortschritt beobachten zu können befanden sich zwischen den Füllöchern Öffnungen in der Kammerdecke, auch zum einführen von Thermoelementen. Auch in der Ofentür befanden sich Meßstutzen und die Planieröffnung war größer dimensioniert um verschiedene Gassammelraumhöhen einstellen zu können.
Zum Beheizen diente ausschließlich Starkgas. Über diverse Meßstrecken konnte der Unterfeuerungsbedarf der gesamten Ofengruppe als auch exakt die Unterfeuerungsgasmenge eines einzelnen, und zwar des dritten Ofens, ermittelt werden. Auch der Heizwert des Unterfeuerungsgases wurde automatisch ermittelt. Der Wärmeverbrauch des dritten Ofens wurde deshalb gesonderte Ermittlung da eine gemeinsam ermittelter Wärmeverbrauch aller 5 Öfen keine genauen Resultate für eine größere Ofengruppe ergeben konnte, da die kleine Ofengruppe über zwei Endheizwände verfügte und daher mehr Unterfeuerungsgas benötigte.
Der Regenerator war wie beim Regelstromofen in zehn Einzelzellen unterteilt. Die Meßstellen für die Abgastemperatur befanden sich in den Kniestücken der Abhitzetöpfe. Auch die Abgaszusammensetzung wurde ermittelt. Die Absaugung der Versuchsöfen geschah über eine getrennte Vorlage, deren Druck durch einen eigenen Vorlagedruckregler konstant gehalten wurde. Das Steigrohr des dritten Ofens war verlängert und an eine zweite kleine Vorlage angeschlossen, dadurch können separate Untersuchungen über die gesamte Garungszeit eines einzigen Ofens erfolgen. Die Untersuchung der Qualität (Heizwert, Dichte usw.) des erzeugten Rohgases fand komplett auf der Druckseite des Gassaugers statt.
Die eingesetzte Kokskohle wurde auf der Schachtanlage Wilhelm der Zeche Königin Elisabeth vorbereitet und in Waggons angeliefert, in einem Tiefbunker entladen und über Gummigurtförderbänder zur Verteilerstation des Kohlenturms transportiert. In dem neu errichteten Kokskohlenturm der Kokerei stand hierfür ein extra eingerichtet Bunker mit 800 t Fassungsvermögen zur Verfügung. Um die Schüttgewichtverhältnisse und andere Analysen durchführen zu können war an diesem Bunker eine Beschickungsversuchskammer mit 44 unterschiedlichen Probeentnahmestellen angebaut worden. Nach der Probenahme wurde die Kohle über Bodenklappen abgelassen und in dem Vorratsbunker wieder eingebracht.
Die zu der Versuchskokerei dazugehörige Kokssieberei war für eine stündliche Leistung von 40 t ausgelegt. Sie verfügte über ein Resonanzschwingsieb zur Separation des Kokses in Grobkoks über 80 mm und Brechkokssorten 80/60 und 60/40 und Kleinkoks kleiner 40mm. Des weiteren Verfügte die Sieberei über eine Verladung und Entstaubung. Hier wurden Untersuchungen zur Koksfestigkeit durchgeführt. Zum Zerkleinern der Koksproben stand ein Laboratoriums-Backenbrecher bereit.
In der Kondensationsanlage wurden die kompletten Gasmengen, die Kondensate und der Teer aus dem Rohgas aller fünf als auch einzeln, des dritten Ofens, erfaßt.
Die Kondensation war für eine stündliche Leistung von bis zu 3000 m3 Rohgas ausgelegt. Sie bestand aus zwei Querrohrkühlern von je 165m² Kühlfläche, einer EGR und einem Teerscheidebehälter. Ein Teermeßbehälter, ein Kondensatnachscheide-Sammelbehälter, ein Dickteerkasten, ein Gassauger sowie Pumpen und Regler komplettierten die Kondensation.
Der Gasweg war über die Vorkühler I und II, die sowohl parallel als auch hintereinandergeschaltet werden konnten, über Elektrofilter zum Gassauger. Dieser regelbare Gassauger ermöglichte über die zweite kleine Vorlage eine getrennte Absaugung des Rohgases des mittleren Ofens.
Das Berieselungswasser, der Teer, das Kondensat aus der Vorlage sowie die Kondensate aus den Kühlern und der EGR wurden in einem Zwischenbehälter und in einer Kondensat-Tiefgrube gesammelt. Von dieser Grube aus wurde das Gemisch mit Pumpen in den Teerscheider gefördert und entwässert. Nach Bestimmung der Menge und Probenzug wurde der entwässerte Teer den Teervorratsbehälter der Kokerei zugeführt. Das abgeschiedene, teerfreie Wasser wurde wieder zur Vorlagenberieselung eingesetzt. Zahlreiche Anzeige- und Schreibgeräte waren in der Kondensationsanlage zu finden, die eine lückenlose Überwachung der Abläufe ermöglichte.
Erwähnenswert ist noch, daß auf dieser Kokerei die erste Schwefelsäure-Naßkatalyse-Anlage in Betrieb genommen wurde. Hierbei handelt es sich um ein Verfahren zur industriellen Herstellung von Schwefel aus Schwefelwasserstoff. Dabei wurde zunächst ein Teil des Schwefelwasserstoffs zu Schwefeldioxid verbrannt. Die bei der Verbrennung entstehenden SO2-Gase wurden bisher immer getrocknet, bevor sie mit dem Katalysator in Berührung kamen. Bei diesem neuen Verfahren verblieb der Wasserdampf in den SO2-Gasen, da festgestellt wurde, daß der Wasserdampf keinen nachteiligen Einfluß auf das Reaktionsvermögen in Gegenwart eines vanadinpentoxydhaltigen Katalysators hatte.



Im Jahre 1964 gehörte die Kokerei zur HOESCH AG Bergbau (Gladbecker Straße 413, 4300 Essen 12). Kokereidirektor war Dr. Hermann Werres und Betriebsleiter Kokereiinspektor Dipl.-Ing. Friedrich Weyer. Im Jahre 1969 wurde die Kokerei Emil in die RAG miteingebracht. Im Jahre 1972 wurden 799460 t Koks produziert und es waren über 350 Mann auf der Anlage beschäftigt. Betriebsführer zu diesem Zeitpunkt war Karl Scheepers. Die Stillegung erfolgte zum 30. Juni 1973. 407 Beschäftige verloren ihren Arbeitsplatz. Mit Hilfe des Anpassungsgeldes, mit Beihilfen nach den Richtlinien des Montanunionvertrages und über die Knappschaftsausgleichsleistung konnten 117 Arbeitnehmer in den Ruhestand treten. Etwa 250 Koker erhielten einen anderen Arbeitsplatz innerhalb der Ruhrkohle AG während 40 Kumpel der Kokerei Emil aus dem Bergbau abkehrten.
Kurz darauf verfolgte der Abbruch der Betriebsgebäude und anlagen. Die so entstandene Freifläche diente der RAG seit etwa 1989 als Kohlenlagerplatz und Verladebahnhof der Bahn und Hafenbetriebe. Nach der Sanierung der Böden, die vorraussichtlich bis Ende 2021 dauert, soll das Gelände dergewerblichen Nutzung zugeführt werden. Der Landabsatz (LKW-Verladestelle) wurde Ende des Jahres 2012 abgebrochen. Heute erinnert nichts mehr an diese einst beeindruckende Kokereianlage.
![]() ![]() ![]() Kohlenbezugs- und Hausbrandbestellkarte sowie Bergmannsbuch des Großvaters Gustav Schönfeld. (© Sammlung Barz/Berg, aus dem Nachlaß Gustav Schönfeld) |
Quellennachweis:
- Dr. A. Spilker, Generaldirektor der Gesellschaft für Teerverwertung Duisburg-Meiderich: "Kokerei- und Teerprodukte der Steinkohle", vierte Auflage, 1923
- Dr. Otto Grosskinsky: "Handbuch des Kokereiwesens", Bd. I und II, Düsseldorf 1958
- Dr. F. M. Ress: Geschichte der Kokereitechnik; Essen 1957
- Jahrbuch für den Oberbergamtsbezirk Dortmund (fortlaufend)
- verschiedene Unterlagen des Stadtarchives Essen
- Prof. Dr.-Ing. Dr. rer. nat. h. c. Wilhelm Reerink, Dr. rer. nat. Kurt-Günther Beck, Dr.-Ing. Wilhelm Weskamp: Die Versuchskokerei des Steinkohlenbergbauvereins, Springer Fachmedien Wiesbaden, 1963
- 25 Jahre Didier-Kogag: Koksofenbau- und Gasverwertungs-A.-G., 1941
© Michaela Barz-Berg
Bild- und Textmaterial sind urheberrechtlich geschützt. Alle Rechte vorbehalten. Die Verwendung der Texte, Bilder oder Graphiken - auch auszugsweise - ohne Genehmigung des Webmasters ist strafbar.