Kokerei Friedrich Thyssen 4/8 - Die weiße Seite
Zum Inhalt:
Kondensation
Gassauger
Teergewinnung
Rohbenzolerzeugung
Benzolreinigungsanlage
Benzoldruckraffination
H2S-Entf. und Schwefelsäureerz.
komb. H2S NH3 Verbrennung
Kondensation.
Die Kohlenwertstoffanlage bestand anfangs aus Teergewinnung, Ammoniumsulfaterzeugung und Rohbenzolgewinnung. Im Jahre 1908 wurde eine Benzolreinigungs- und Redestillationsanlage in Betrieb genommen. in dieser Anlage wurde das Benzolvorerzeugniszur Entfernung der Reaktionsprodukte noch einmal destilliert. Das bis Mitte der 20er Jahre angewandte Verfahren war das indirekte Verfahren. Nach dem Umbau kam das halbdirekte Verfahren von Koppers in Anwendung. Die Kokerei verarbeitete nicht den gesamten Gasanfall, ein Teil des Gases wurde ab Vorlage an die Thyssenschen Gas- und Wasserwerke GmbH geliefert. Erst ab Ende der 30er Jahre wurde das gesamte Rohgas auf der Kokerei verarbeitet, nachdem die vorhandene Nebengewinnungsanlage der Thyssenschen Gasgesellschaft stillgelegt wurde. Die bei der Aufarbeitung des Rohgases auf Leuchtgas anfallenden Nebenprodukte in Form von Teer, Ammoniakrohwasser und benzolangereichertes Waschöl wurde bis zu diesem Zeitpunkt an die Kokerei zurückgeliefert.Nach dem Umbau durch Koppers standen für die Kühlung des Rohgases für die Batterien I und II vier Reutterkühler von je 409 m² Kühlfläche und zwei Reutterkühler von je 100 m² Kühlfläche, für die Batterien III und IV 6 Reutterkühler von je 1000 m² Kühlfläche und für die Batterien V und VI zwei Reutterkühler von je 345 m² Kühlfläche zu Verfügung. Diese Gaskühlanlage wurde im Jahre 1957 bzw. 1959 gegen moderne Intensivgaskühler ausgetauscht. Ein neuer Gasschlußkühler wurde 1953 vor der Benzolauswaschanlage errichtet und ein dritter Vorkühler wurde im Jahre 1966 neben dem Maschinenhaus zu den zwei vorhandenen aufgestellt. Ebenfalls im Jahre 1966 wurde eine elektrostatische Gasreinigung (EGR) bestehend aus Filtern errichtet.

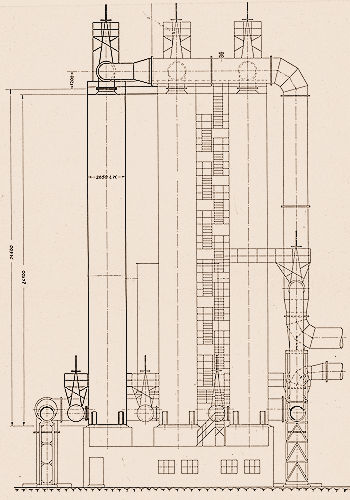
Aufstellung des dritten Vorkühlers, 07.1966
(© Sammlung Barz/Berg)
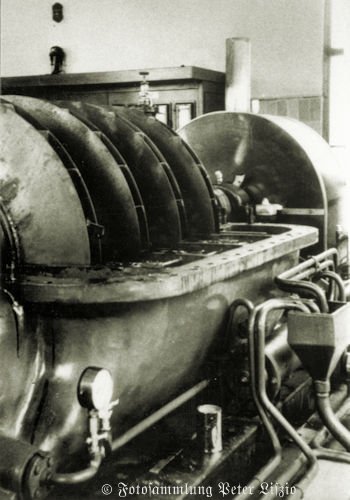
(© Fotosammlung Peter Liszio,
Kokerei Schwelgern)
Gassauger.
Für die Gasbewegung sorgten seit den 20er Jahre fünf Gassauger, wobei die Maschinen 1, 2 und 5 eine Stundenleistung von 12.500 m³, Nr. 3 von 25.000 m³ und Nr. 4 von 8300 m³ hatten. Im Jahre 1938 kam ein weiterer Gassauger von 8040 m³ hinzu. In den Jahren 1953 und 1955 wurden modernere Turbogassauger beschafft. Im Jahre 1959 kam eine Gegendruck-Dampfturbine hinzu, die nach der Stillegung an die Kokerei Osterfeld abgegeben wurde.Nach dem halbdirekten Verfahren folgten hinter den Saugern die Sättiger und anschließend die Schlußkühler, die als Hordenkühler ausgebildet waren. Im Anschluß hieran wurde das Gas durch die Benzolwascher geleitet, von denen - man mag es kaum glauben - 20 vorhanden waren. Im Jahre 1938 wurden diese Waschanlage für Benzol durch Aufstellen größerer und leistungsfähigerer Wascher erneuert. Nach Verlassen der Benzolwascher wurde das Gas den Verbraucherwerken zugeführt.
Teergewinnung.
Sämtliche Kondensate der Kondensation wurden in drei Teerscheidebehälter (zwei zu 350 und einer zu 400 m³ Inhalt) in Teer und Kohlewasser getrennt. Der Teer floß zwei Teerentwässerungsbehälter von 400 bzw. 100 m³ Inhalt zu und wurde anschließend in vier Teerverladebehälter gepumpt. Im Jahre 1953 wurde die Teergewinnung modernisiert. Teerscheider und Teerbehälter wurden erneuert und eine Teerdruckentwässerung wurde in Betrieb genommen.Das Kohlewasser wurde, bevor es zu den Abtreibern weitergeleitet wurde, zunächst entphenolt. Dies geschah in einer von der Fa. Koppers gebauten Anlage nach dem Benzol-Lauge-Verfahren. Im Jahre 1965 wurde eine Phenosolvan-Anlage mit einem Durchsatz von 600 m³/Tag in Betrieb genommen.
In der Abtreiberanlage wurde das Ammoniak aus dem Kohlewasser abgetrieben. Die Abtreiberschwaden wurden vor dem Sättiger dem Rohgas zugeführt und dieses Gas-Dämpfe-Gemisch wurde im Sättiger durch ein Schwefelsäurebad geleitet, wobei schwefelsaures Ammoniak (NH3)2SO4, auch Ammoniumsulfat genannt, entstand, ein Düngesalz. Es standen fünf Sättiger zur Verfügung, von denen für gewöhnlich drei in Betrieb waren. Für jeden Sättiger waren zwei Zentrifugen vorhanden. Nachdem das Salz in den Zentrifugen trockengeschleudert worden war, wurde es in die Salzlager (1904 errichtet) gebracht. Die Salzverladung wurde im Jahre 1939 modernisiert. Das Ammoniaksalz wurde über die Fa. Ruhrstickstoff AG abgesetzt.
Für die Herstellung von verdichtetem Ammoniakwasser standen zwei Verdichteranlagen zur Verfügung. Hier wurden die aus den Abtreibern entweichenden Dämpfe, die Brüden, durch Kühlung zu sog. verdichtetem Ammoniakwasser kondensiert. Die stündliche Leistung betrug je Anlage 500 l 20%iges Ammoniakwasser.
Rohbenzolerzeugung.
Das von den Benzolwaschern ablaufende angereicherte Waschöl gelangte zur Leichtölgewinnungsanlage, die von der Fa. Hinselmann 1929 errichtet wurde. Das gesättigte Öl wurde in vier Wärmetauscher vorgewärmt und anschließend in drei Ölerhitzern indirekt auf 130° C erhitzt. Im Jahre 1953 wurde ein gasbeheizter Röhrenofen zur Erhitzung des Waschöls als Ersatz für die alte Ölerhitzeranlage in Betrieb genommen. In den nun folgenden Abtreibern wurde das Benzol mit direktem Dampf abgetrieben wobei die obere Hälfte des Abtreibers dabei als Rektifizierkolonne für die aufsteigenden Destillationsdämpfe diente. Die den Abtreiber verlassenden Dämpfe wurden kondensiert und in Vorprodukt und Wasser nach ihren spezifischen Gewichten geschieden. In der Nebenkolonne wurde dieses Benzol-Vorprodukt nochmals erhitzt und verdampft. Auf dieser Kolonne befand sich ein Dephlegmator (Rückflußkühler), welcher die Aufgabe hatte, das Öl und Naphthalin in die Kolonne zurückzuführen.Das so gewonnene Leichtöl konnte ohne Vordestillation gereinigt werden.
Das abgetriebene Öl wurde gekühlt um es wieder zum auswaschen verwenden zu können. Im Mai 1954 wurde eine
Waschölentpechungskolonne in Betrieb genommen, die einer Verdickung des Waschöls entgegenwirkte, da verdicktes Öl
ein verringertes Aufnahmevermögen besaß. Durch diese Regenerierung konnte der Waschölverbrauch um etwa 1/6 gesenkt werden.
Benzolreinigungsanlage.
Die Benzolreinigungsanlage, errichtet im Jahre 1928, verarbeitete nicht nur das selbst produzierte Rohbenzol sondern auch das Rohbenzol der Kokerei Friedrich Thyssen 3/7, der Kokerei Westende und der Kokerei der Hütte Vulkan. Das Rohbenzol wurdezunächst einer Vorwäsche und anschließend einer Schwefelsäurewäsche unterzogen. Zuallererst wurde es jedoch in zwei Rohbenzol-Mischbehälter (1955) von je 150 m³ Inhalt zur Erzielung eines gleichmäßigen Einsatzes gemischt. Zur Schwefelsäurewäsche wurde das Benzol in großen Rührgefäßen eingesetzt und das notwendige Reagens, 66er Schwefelsäure, wurde während des Rührvorganges langsam zugesetzt. Auf diese Weise wurden die ungesättigten Verbindungen durch Polymerisation neutralisiert und die sogenannten Harzbildner aus dem Rohbenzol entfernt. Nach etwa halbstündigem Rühren ließ man der Waschflüssigkeit ebenso lange Zeit sich von dem Rohbenzol abzusetzen und zog dann die Waschflüssigkeit möglichst scharf ab. Das rohe Benzol mußte nun mit Wasser, anschließend mit verdünnter Natronlauge und abschließend nochmals mit Wasser nachgewaschen werden. Bei diesem Arbeitsvorgang fiel das Cumaronharz als Nebenprodukt an. Die Abfallschwefelsäure wurde nach dem Abziehen aus dem Rührwerk mit Ammoniakwasser neutralisiert und anschließend in der Ammoniakfabrik weiterverarbeitet.Das in der Schwefelsäurewäsche vorgereinigte Rohbenzol mußte nun in einzelne Fraktionen übergeführt und gereinigt werden. Die hierfür notwendige Destillation erfolgte in acht großen, liegenden schmiedeeisernen Blasen mit 33,5 t Fassungsvermögen. An jeder Blase war eine Kolonne mit Kondensator angeschlossen. Ein Dephlegmator lieferte den erforderlichen Rückfluß, mit dem der aufsteigende Dampf intensiv in Berührung kam, um die Trennwirkung zu erhöhen. Die aus diesem Rückflußkühler austretenden Benzoldämpfe wurden in dem Röhrenkondensator niedergeschlagen und gekühlt. Die einzelnen Fraktionen wurden einzeln nacheinander abgenommen (diskontinuierliche Destillation).
Es wurden folgende Fraktionen hergestellt:
- 90er Benzol (Handelsbenzol I)
- gereinigtes Toluol
- Lösungsbenzol I
- Lösungsbenzol II
- gereinigtes Toluol
Benzoldruckraffination.
Im Jahre 1959 wurde die Schwefelsäureraffination die teilweise über 10 % Raffinationsverlust mit sich brachte, durch das Benzoldruckraffinationsverfahren ersetzt. Hierbei wurden die im Rohbenzol enthaltenen ungesättigten Verbindungen durch Anlagerung von Wasserstoff bei 60 atü und hoher Temperatur abgesättigt. Als Wasserstoffspender und Katalysator diente Koksofengas, wobei dieses "Kreislaufgas" regelmäßig aufgefrischt werden mußte. Das verbrauchte, wasserstoffarme Gas wurde für Heizzwecke innerhalb des Werkes verwandt. Das Druckraffinat wurde anschließend in einer Lauge- und Wasserwäsche von Schwefelwasserstoffresten befreit. Anschließend wurde es durch Destillation zu Reinbenzol verarbeitet. Die hierfür nötige Anlage bestand aus Röhrenofen, der Hauptkolonne mit Kühlern und Wärmetauschern sowie Nebenkolonne mit dem Erhitzer. In der Hauptkolonne wurde das Benzol wie auch die leichter siedenden Kohlenwasserstoffe abdestilliert und in der Nebenkolonne die wiederum die leichter siedenden Kohlenwasserstoffe, so daß in der Nebenkolonne das Reinbenzol zurückblieb und in der Hauptkolonne die schwerer als Benzol siedenden Kohlenwasserstoffe.Schwefelwasserstoffentfernung und Schwefelsäureerzeugung komb. H2S NH3 Verbrennung.
Im Mai 1971 wurde eine nach dem Verfahren der Fa. Still arbeitende Anlage für kombinierte H2S/NH3-Verbrennung und Schwefelsäureerzeugung in Betrieb genommen. Hierfür mußte eine Schwefelwasserstoffentfernungsanlage (NASS ND) bestehend aus zwei Waschern, Abtreiber und Entsäurer, Kühler- und Wärmetauscher und die notwendige Meßwarte errichtet werden. So entfiel die wenig rentable Ammoniumsulfatgewinnung. Sie war mit der

komb. H2S NH3Verbrennung
der Kokerei August Thyssen baugleich.
Eine regelmäßige Qualitätskontrolle der Produkte erfolgte im Betriebslaboratorium, das im Jahre 1946 errichtet wurde.
Quellennachweis:
- verschiedene Unterlagen aus der Privatsammlung Barz/Berg zur Stillegung der Kokerei Fr. Thysssen 4/8
- Dr. A. Spilker: "Kokerei und Teerprodukte der Steinkohle", Halle (Saale), 1933
- Der Bergbau der Hüttenwerk Oberhausen AG, Oberhausen Rheinland, 1961
- Dr. Otto Grosskinsky: "Handbuch des Kokereiwesens", Bd. II, Düsseldorf 1958
- verschiedene Akten der Gruppe 611 des Duisburger Stadtarchivs zu baulichen Maßnahmen der Kokerei Fr. Thyssen 4/8
© Michaela Barz-Berg
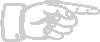
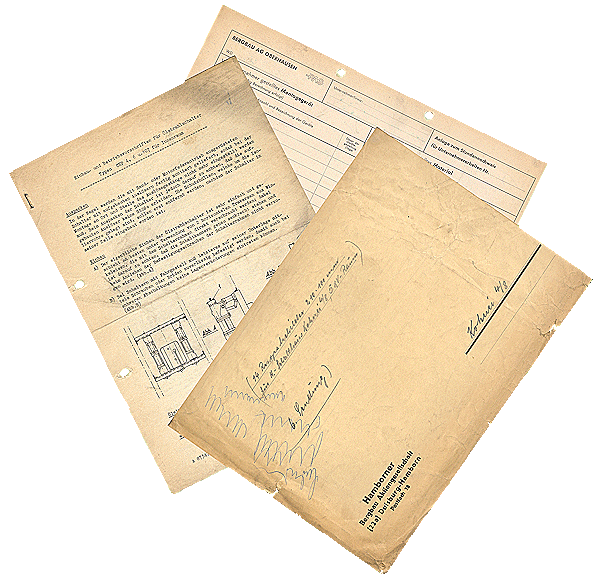
Bild- und Textmaterial sind urheberrechtlich geschützt. Alle Rechte vorbehalten. Die Verwendung der Texte, Bilder oder Graphiken - auch auszugsweise - ohne Genehmigung des Webmasters ist strafbar.